WHAT CAN THE SPS PROCESS DO?
SPS has achieved significant improvements in the synthesis and processing of new advanced materials,
especially in the following four areas: (1) Sintering Technology for rapid, grain boundary controlled and
temperature gradient sintering, (2) Bonding Technology for bonding dissimilar/similar, graded and solid-solid
materials, (3) Surface Treatment Technology for the modification and surface hardening of plasma spray coated
layers and (4) Synthesis Technology for solidification of polymers, growth of single crystals, synthesis of
eutectic substances and other processes. SPS also offers advantages as a production technology for numerous
other applications in addition to materials synthesis.
Example.1 | The SPS technology features quick temperature rise by self-heating now making possible the processing of compacts without degrading their original characteristics, which is difficult by conventional sintering. The crystalline structure of such compacts offer very high accuracy thanks to their Near-Net-Shape sintering. |
---|---|
Example.2 | SPS has achieved favorable results in the synthesis of a wide range of ceramics, cermets, and metallic materials. Sintered materials include amorphous and electronic materials that are easily degraded if processed at high temperatures. Highly active metals such as titanium and aluminum, various FRCs (fiber reinforced ceramics) such as zirconia and alumina containing whiskers and fibers, super-conducting, metallic FRMs (fiber reinforced materials), magnetic materials, hard alloys and other such materials have also been successfully processed. |
Example.3 | SPS has gained an excellent reputation by making practical the synthesis of functionally graded materials (FGMs), inter-metallic materials and sinter-bonding of dissimilar materials such as metal and glass. In the field of energy conversion, SPS has also succeeded in the modularization of bismuth telluride (BiTe) for Pertier modules and Seebeck thermoelectric semiconductor chips as well as germanium-silicon(SiGe), iron-silicon (FeSi) and manganese-silicon materials (MnSi). |
Example.4 | The SPS process has also been successful in sintering rapidly solidified AlSi aluminum powders considered difficult to sinter because of their fine micro structures at the nanometric level. With SPS, compacts of these materials to a relative density of almost 100% from the powder phase is possible while maintaining the nanometric structure in only a few minutes. When these pre-forms are rapidly forged, they reach superplasticity 100 times faster than previously obtained speeds and are thus suitable for mass-production of 3D-shaped components. |
Example.5 | High wear-resistant nozzle parts fabricated from fine ceramics by the 3D Near-Net-Shape forming SPS process technology are now available. Thanks to the superior technology, these nozzles can be used for abrasive applications that require no additional polishing or grinding. |
TYPICAL APPLICATIONS FOR SPS
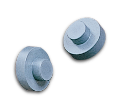


- 1.Ceramics
- Oxides, Carbides, Nitrides,
Borides, Fluorides - 2.Polymer
- Polymide, Nylon, Polyethlene
- 3.Composite Materials
-
Fiber-Particle Compounded Composite Materials,
Functionally Graded Materials,
Bonding of dissimilar - 4.Metals
- Hard Metal Alloys, Amorphous Materials,
Magnetic Materials, Intermetallic Compounds - Others
- Cermets, Intermetallic compounds